Our services
AMufacture operates an ecosystem of best-in-class production and finishing facilities with end-to-end part traceability and repeatability. Our dedicated assembly lines serve as an extension to your workflow, delivering parts to your specifications.
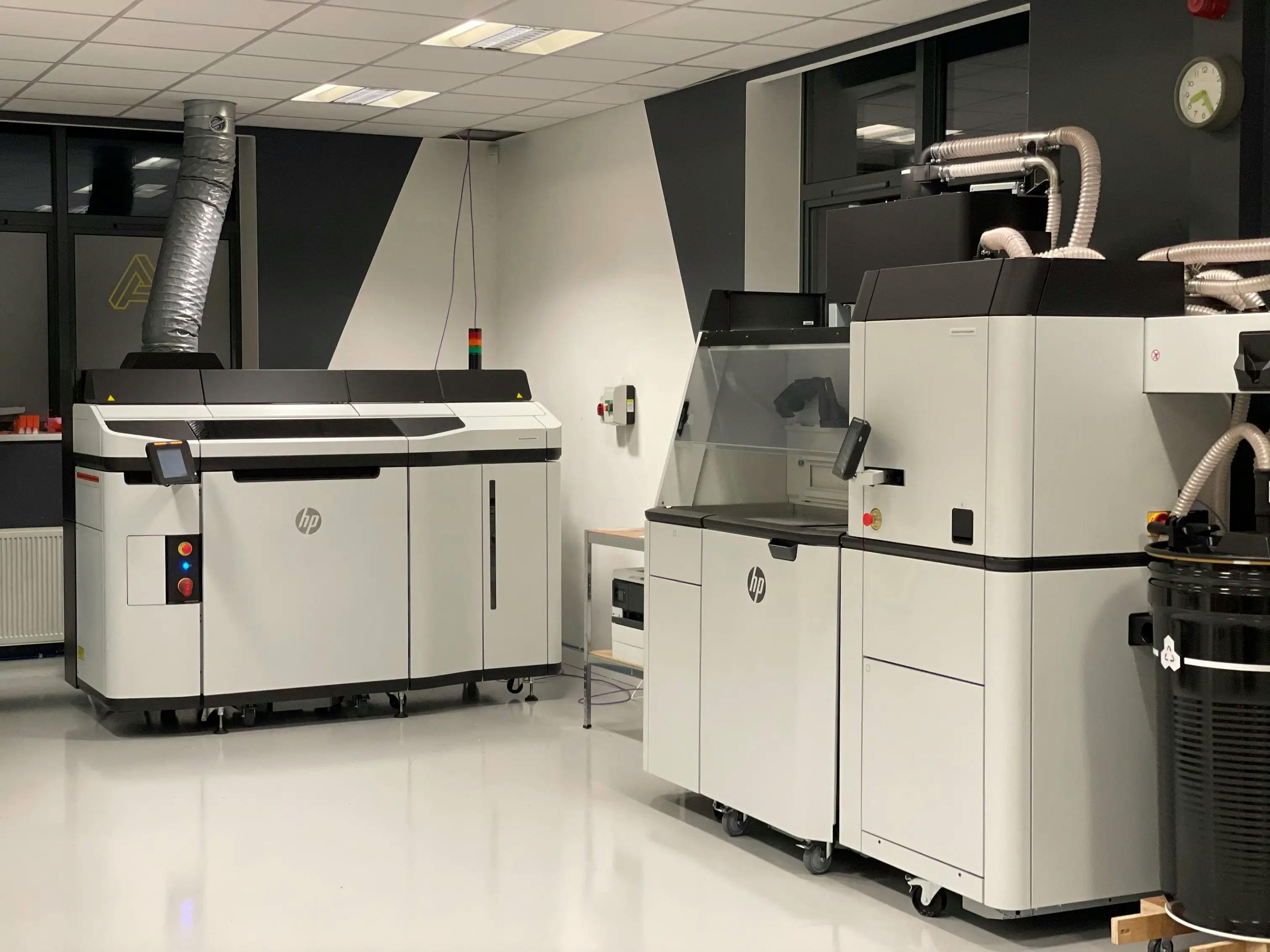
Our 3D printing technologies
What is the right solution for your business?
Collaborate with AMufacture's in-house specialists to understand how additive manufacturing can optimise your workflow and advise which technology solution, material and finishing suits your requirements.
As your contract manufacturing partner, we offer a wide range of 3D printing technologies and materials, including in-house capabilities with MJF, DLP, SLS, SLA and FDM. We also operate and manage traditional manufacturing processes such as CNC and injection moulding.
We specialise in HP Multi Jet Fusion (MJF) as this technology meets the high specifications and requirements of our clients with respect to part performance, scalability and lead time.
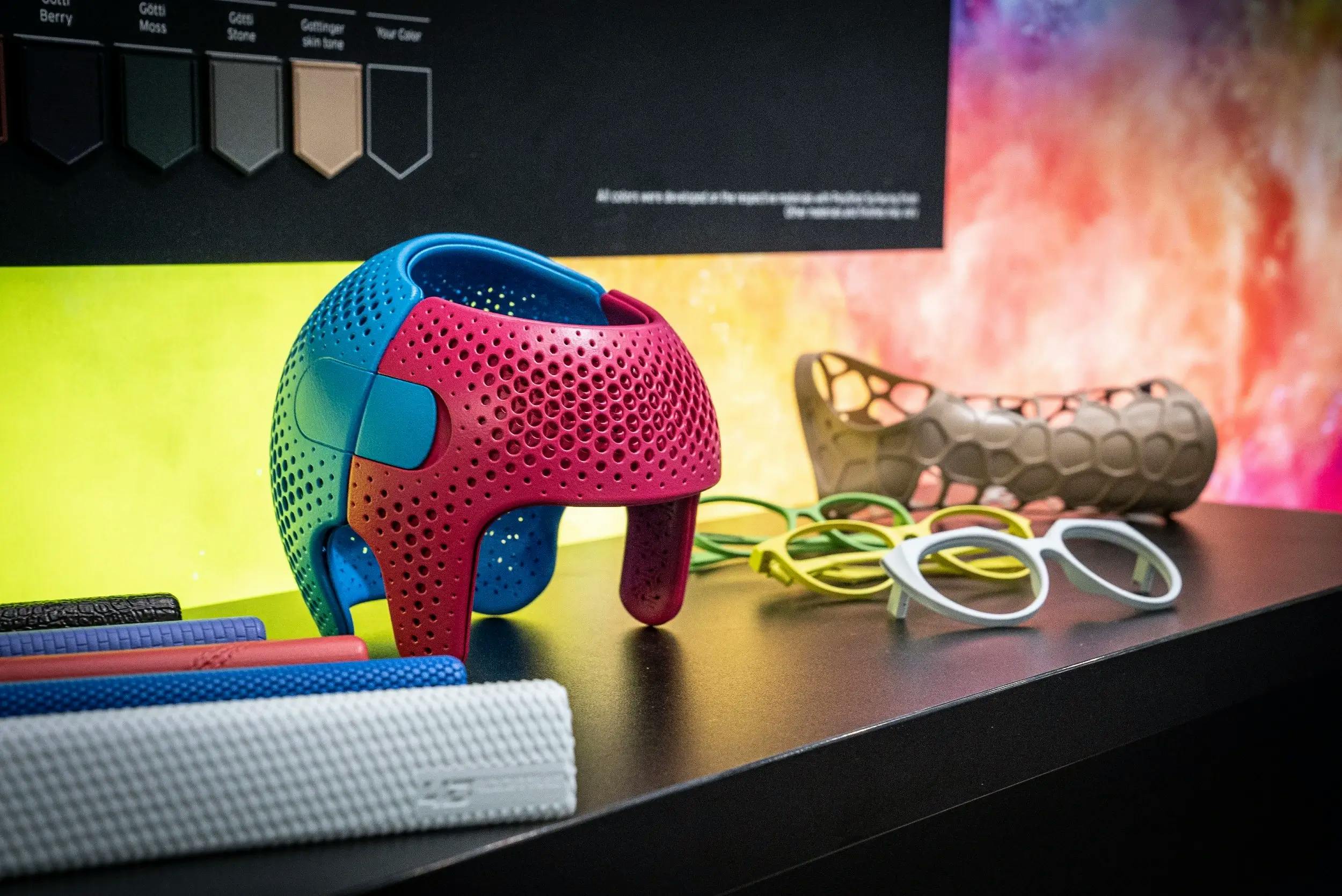
Durable engineering grade materials
AMufacture specialises in the use of engineering materials, with a focus on HP 3D High Reusability Nylon PA12 and HP PA12 White. This provides design freedom for our clients to develop functional end-use isotropic parts, capable for production at scale.
Other engineering grade materials are offered by AMufacture to meet your specifications (including PA11 and TPU), please contact us for more information.
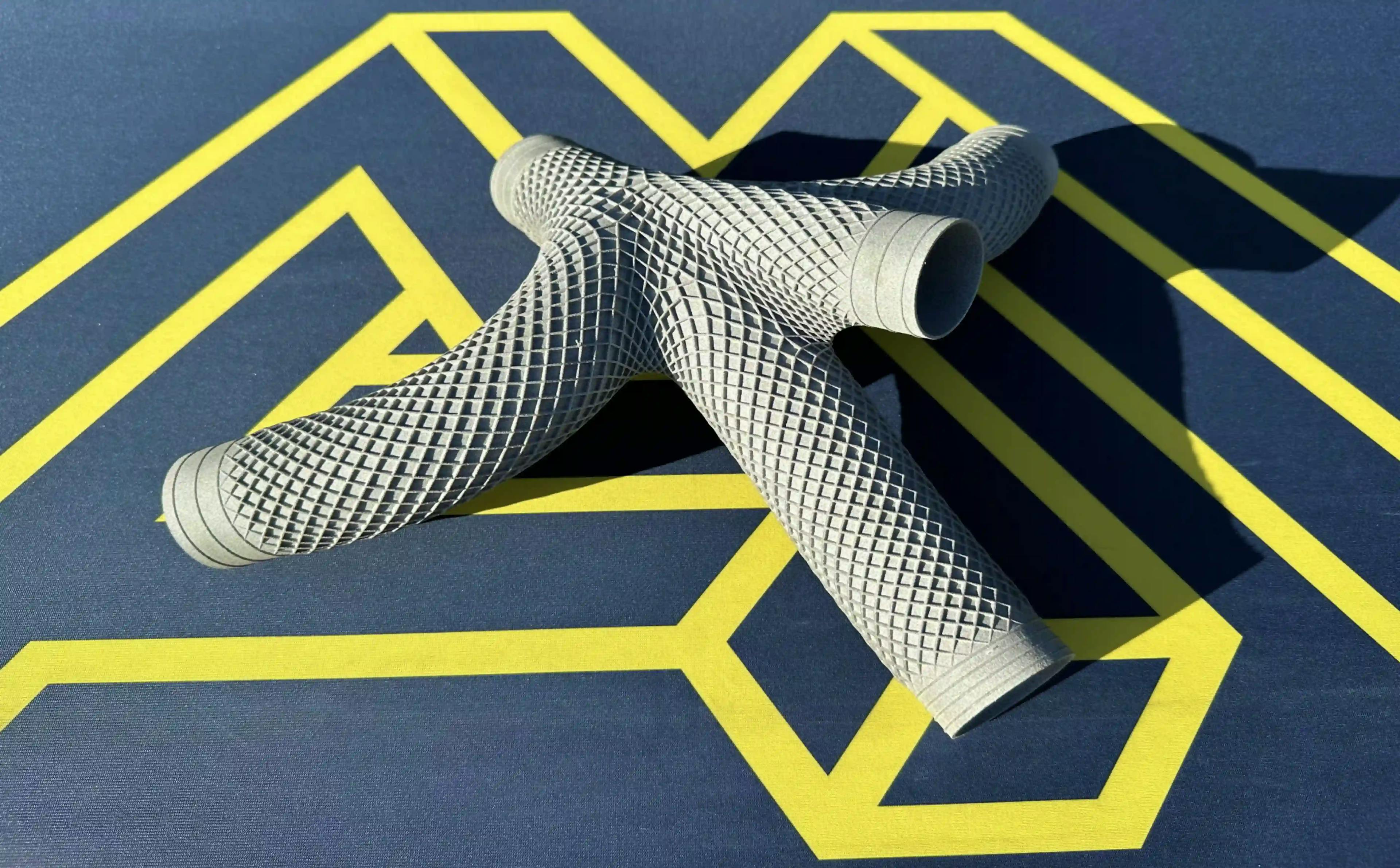
Some of our industry applications:
Marine
AMufacture's expertise in the marine industry has been driven by co-founder and COO, Will Howden, a qualified naval architect after a successful Olympic sailing career.
Our experience working within this sector has involved design optimisation and manufacturing of parts to be included in luxury and racing yachts to commercial vessels. Part applications range from pedal mechanisms and grey water manifolds to water strainers and external painted parts.
As a Tier 1 supplier, AMufacture has developed specialised quality controlled workflows to adhere to the strict specifications relating to marine part performance, aesthetics and scaled production. To meet this demand, AMufacture has expanded in-house capabilities and expertise, which have now been applied across clients and sectors.
Marine
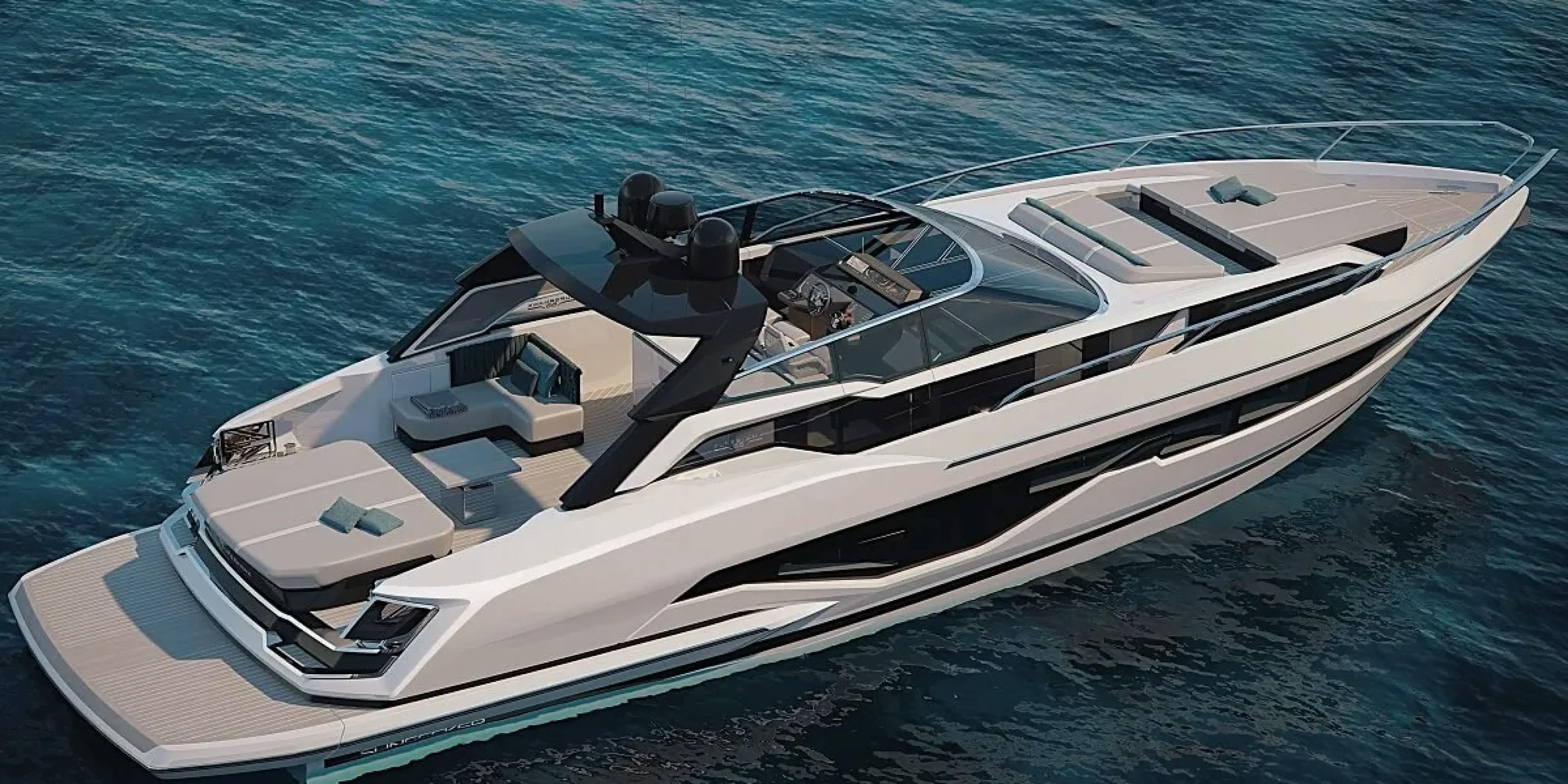
Automotive
AMufacture has experience in collaborating with major automotive OEMs to optimise pre-production, bridge and ramp-up production. Our capabilities range from prototype parts and interior cockpit plastics to full HVAC systems, general air ducts, break ducts, under bonnet components, cable saddles and hose saddles.
Additive manufacturing technology has successfully been integrated within automotive production at scale, recently demonstrated by Toyota's first mass-produced 3D printed certified part. This was the automatic transmission oil cooler ducts manufactured through MJF technology, included within the Lexus LC500, using 37% less greenhouse gas emissions compared to injection moulding.
Automotive
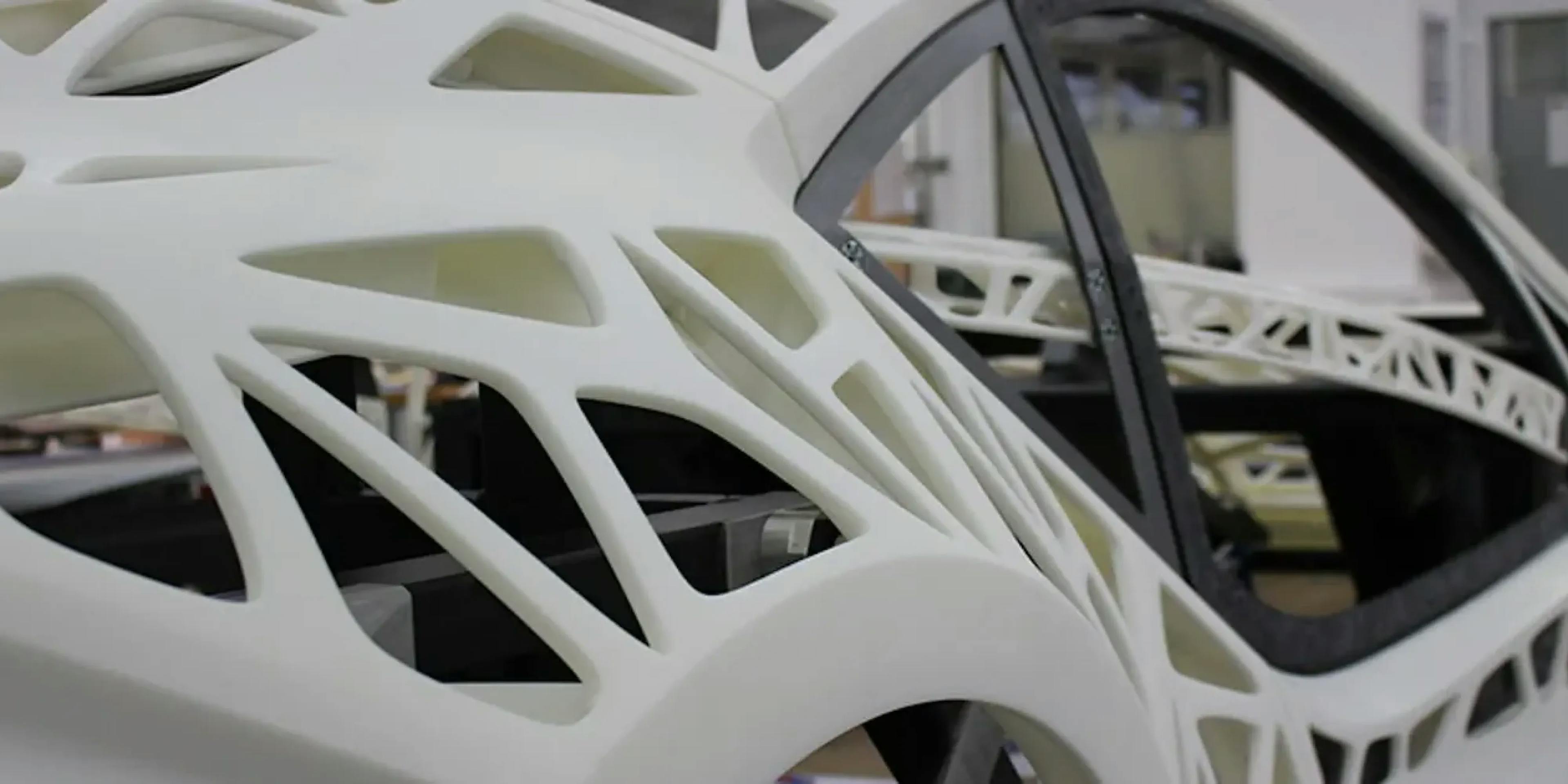
Medical
Additive manufacturing has been able to accommodate the personalised treatments required throughout the healthcare sector.
AMufacture has expertise collaborating with clinicians for on-demand custom manufacturing services, with repeatable production available to patients. Applications include prosthetics and orthotics, with clients ranging from paralympic athletes to infants suffering from plagiocephaly requiring cranial moulding orthoses.
A modern or traditional scanned file, for instance an MRI, can be converted into a printable CAD file by our design team, with customisable corrective adjustments if necessary. AMufacture is able to deliver high-performance, functional and repeatable parts that can be printed at a comparatively lower cost and lead time than traditional healthcare manufacturing. These parts are stored within your Digital Warehouse, enabling seamless repeat orders and on-demand design adjustments if required to suit your patients' needs.
Medical
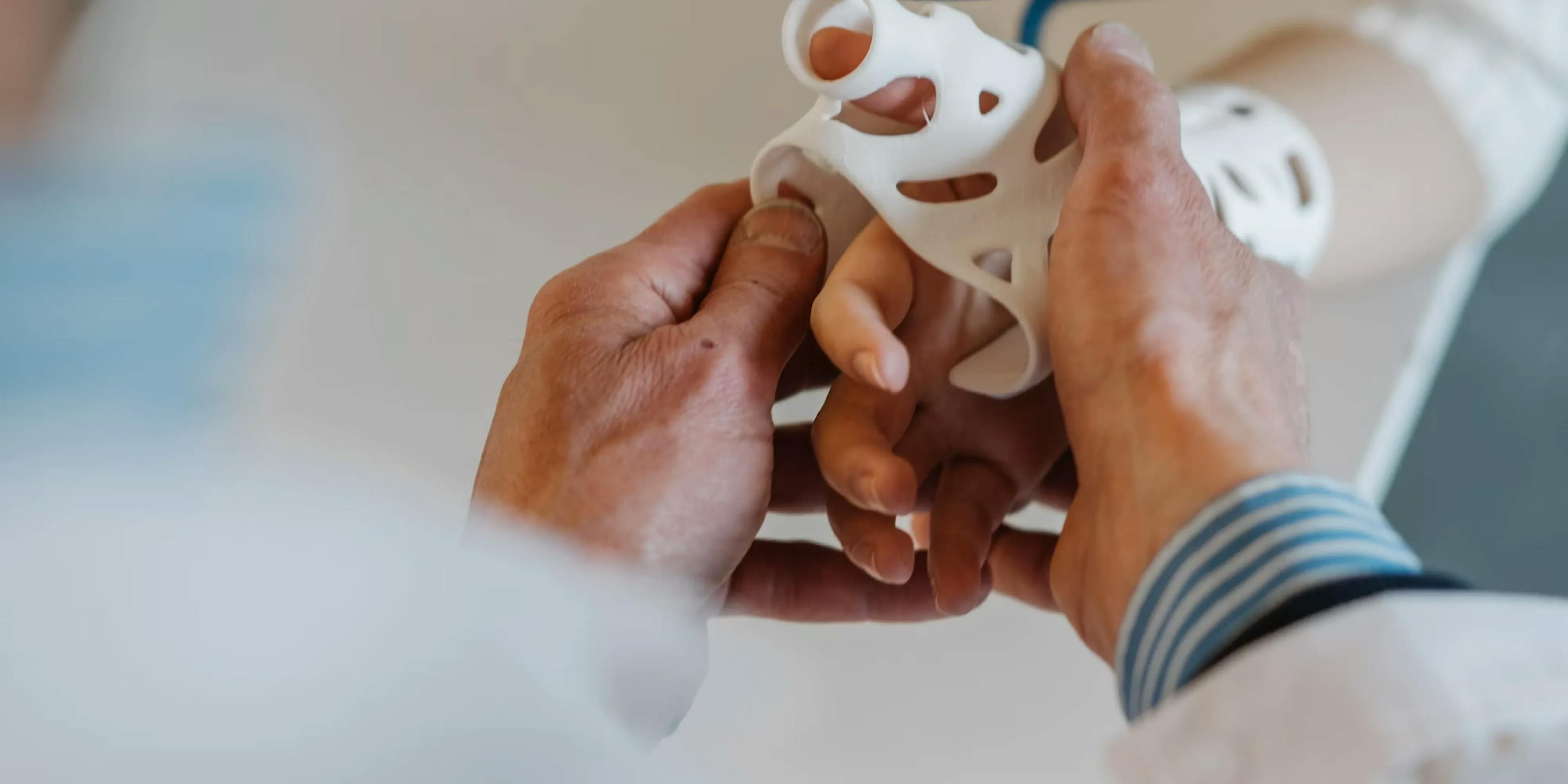